News classification
Contact us
- Add: ChanFu Dong Road,XiaoBian Village, ChangAn Town,DongGuan City,GuangDong,China
- Tel: +8613652508770(Jerry )
- Fax: 0769-23094426
- Email: [email protected]
How do Pogo pins work?
How do Pogo pins work?
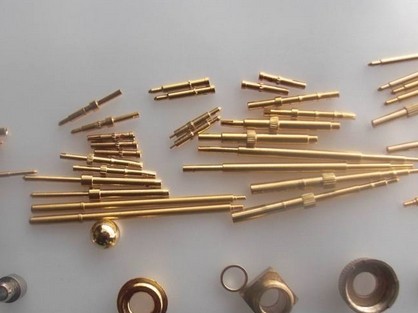
The working principle of Pogo Pin (spring probe) is based on the coordinated cooperation of its precision mechanical structure and electrical performance design, and stable current and signal transmission is achieved through elastic contact. The following is a detailed description from the dimensions of structural operation mechanism, electrical conduction path, dynamic compensation mechanism, environmental adaptability, etc.:
I. Basic structure and coordinated operation principle
Pogo Pin consists of three core components:
1. Plunger: Usually made of brass or stainless steel, the front end is processed into a bevel or spherical surface (contact angle 30°-60°), and the tolerance is guaranteed by CNC precision cutting. The thickness of the gold plating layer on the surface is 0.3-0.8μm to reduce the contact resistance. This component is responsible for the physical contact with the docking terminal and maintains the stability of the contact point within the Pogo pin compression stroke.
2. Tube: The outer diameter ranges from 0.6-2.5mm, and the inner wall is mirror polished, which serves as the main channel for current transmission. Some high-end models use copper-nickel-zinc alloy with a conductivity of 28% IACS and a high yield strength (≥600MPa) to resist deformation.
3. Spring: SUS304 or piano steel wire (diameter 0.05-0.2mm) is selected, and the elastic modulus is maintained at 190-210GPa after heat treatment. The initial preload of the spring is 0.5-5N, and the plug-in life can still maintain 80% of the initial pressure after 100,000 times.
Workflow:
1. Preload stage: The needle is pushed into the needle tube by external force, and the spring is compressed to 1/3~2/5 of the initial length (typical stroke 0.3-3.5mm), at which time the spring force reaches the rated value.
2. Contact conduction: The needle bevel and the inner wall of the needle tube form an Ω-shaped contact loop (contact area ≥0.2mm²), and the current is transmitted along the path of needle → needle tube → PCB pad.
3. Dynamic compensation: Under vibration or thermal expansion conditions, the spring continuously applies vertical compensation force (change rate within ±0.5mm stroke ≤8%) to maintain contact resistance <50mΩ.
2. Optimization of current conduction path
The conduction path design directly affects the electrical performance. The main technical solutions include:
1. Beveled surface conduction mode (accounting for 85% of applications): The needle is processed into a 45° beveled surface to form a surface contact (rather than a point contact) with the wall of the needle tube, which increases the current conduction area to 3 times the original and reduces the contact resistance to 2-10mΩ (common structure>20mΩ). Test data of a 5G mobile phone antenna shows that this design reduces the signal insertion loss by 0.6dB@28GHz.
2. Dual-channel conduction design: Cnomax high-end Pogo Pin adopts a hollow needle tube structure (inner diameter 0.15mm), and sets a secondary conduction column in the center of the needle to form an inner/outer dual current path, which can increase the transient current carrying capacity to 50A.
3. Spring current avoidance technology: Through special processing, the current bypasses the spring (a component with poor conductivity), and a copper-nickel alloy guide plate is set inside the needle tube, and the current loss rate is reduced from 12% of the conventional structure to 0.5%.
3. Mechanical compensation mechanism
1. Linear pressure curve: The ideal spring stiffness K value range is 2-10N/mm, and the pressure change in the compression stroke is highly linear (R²>0.998), ensuring that the contact force under different compression amounts is predictable. For example, the initial pressure of a TWS headset charging contact is required to be 1.8N±0.2N, and the pressure rises to 3.5N±0.3N at a stroke of 1mm.
2. Three-dimensional self-calibration capability: The spherical structure of the needle head allows a deflection tolerance of ±5°. When the docking terminal is offset, the contact point automatically slides to the geometric center, and the lateral misalignment compensation amount is 0.3mm.
3. Impact absorption mechanism: In a high-frequency vibration environment (such as a car engine compartment), the spring as a damping element can absorb mechanical energy in the 7-11kHz frequency band, and the amplitude attenuation rate is ≥70%, preventing micro-motion wear of the contact point.
IV. Reliability guarantee under special working conditions
1. Anti-corrosion design:
• Multi-layer plating process: bottom nickel plating (3-5μm) enhances adhesion → middle palladium plating (0.5μm) blocks diffusion → surface gold plating (0.3μm) reduces resistance, extending the salt spray test life from 72h of ordinary plating to 1000h.
• Titanium nitride coating: Medical-grade Pogo Pin deposits 2μm TiN coating on the surface, and the acid and alkali resistance is improved by 50 times, meeting the ISO 10993 biocompatibility standard.
2. Waterproof sealing technology:
• Silicone secondary injection molding: The outside of the needle tube is coated with LSR liquid silicone with a hardness of 50 Shore A, which is interference fit with the shell to form an IP68-level seal with a water pressure resistance of 2atm.
• Nano-coating technology: Plasma-enhanced chemical vapor deposition (PECVD) is used to form a 10nm thick diamond-like carbon film on the contact surface, and the contact resistance is only increased by 3mΩ, while achieving a hydrophobic angle of >120°.
V. Signal transmission enhancement solution
1. RF signal optimization:
• Coaxial structure: The distance between the center conductor (needle) and the outer shielding layer (needle tube) is controlled at 0.1-0.3mm, and the characteristic impedance is matched at 50Ω±5%, supporting 40GHz millimeter wave transmission.
• Dielectric filling: PTFE foam with a dielectric constant εr=2.1 is injected into the needle tube cavity to reduce signal attenuation to 0.15dB/cm@10GHz.
2. High-speed digital signal support:
• Structural optimization: Reduce the needle length to less than 0.8mm, shorten the delay difference of the signal path (<5ps), and meet the rise time requirements of the USB4 protocol for 20Gbps signals (≤35ps).
• Impedance compensation: Design compensation capacitor (0.1-0.5pF) at the PCB end to offset the parasitic inductance (0.3-0.8nH) introduced by the Pogo Pin.
VI. Impact of manufacturing process on performance
1. Precision assembly process:
• Automatic riveting: Use a servo press (accuracy ±0.01N) to pre-compress the spring and control the compression amount within ±3% of the nominal value.
• Laser welding: Use 1070nm fiber laser to weld the needle tube and the base, the weld depth-to-width ratio reaches 8:1, and the tensile strength is >300N.
2. Detection technology upgrade:
• Four-wire resistance test: Detect contact resistance at a constant current of 10mA with a resolution of 0.1mΩ.
• X-ray detection: Scan the internal structure with a focus size of 3μm to identify spring deformation or assembly defects.
Currently, Cnomax Pogo Pin is developing towards intelligent sensing. Some products integrate temperature sensors (Pt100 thin film resistors) and stress detection modules (MEMS piezoresistive units) to achieve real-time monitoring of connection status. The continuous optimization of its working principle has made it play an irreplaceable role in aerospace, autonomous driving, wearable devices and other fields.