News classification
Contact us
- Add: ChanFu Dong Road,XiaoBian Village, ChangAn Town,DongGuan City,GuangDong,China
- Tel: +8613652508770(Jerry )
- Fax: 0769-23094426
- Email: [email protected]
Can magnetic connectors work in high temperature environments ?
Can magnetic connectors work in high temperature environments ?
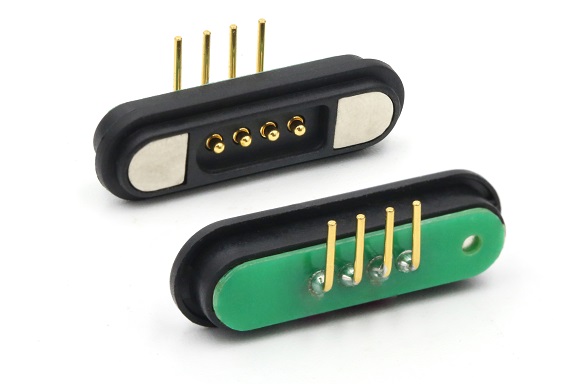
Cnomax Magnetic connectors, also known as magnetic charging connectors or magnetic pogo pin connector are widely used in a range of modern electronic devices—from smartphones, laptops, and smartwatches to industrial machinery, medical instruments, and aerospace systems. Their primary benefits include ease of connection, secure attachment via magnetic force, durability, and the ability to support blind-mating and fast disconnection under strain.
However, when these connectors are intended for use in high-temperature environments, their performance and reliability are put to the test. Extreme heat conditions—such as those found in automotive electronics, industrial furnaces, aerospace systems, or outdoor installations—pose specific challenges to connector design. These challenges center around thermal stability, material degradation, contact resistance, and magnetic performance.
In this article, we will examine in detail whether magnetic connectors can function reliably in high-temperature environments, what factors influence their performance under such conditions, and how they can be designed to meet stringent thermal requirements. We’ll also explore relevant use cases, design strategies, material considerations, and long-term reliability aspects.
1. The Challenge of High-Temperature Operation
High-temperature environments are typically defined as conditions where temperatures exceed 85°C and can range up to 200°C or more, depending on the application. For magnetic connectors, this presents challenges in four primary areas:
A. Thermal Stability of Magnetic Materials
The permanent magnets inside the connectors—typically made of neodymium iron boron (NdFeB), samarium cobalt (SmCo), or ferrite—are essential to ensure secure docking. These materials, however, have different temperature ratings:
Neodymium magnets: High magnetic strength but relatively low maximum operating temperature (usually 80°C to 120°C).
SmCo magnets: Lower magnetic force than NdFeB but excellent thermal resistance (up to 250–300°C).
Ferrite magnets: Moderate heat resistance (50~250°C) and low cost but significantly weaker magnetic pull.
If a magnet is exposed to temperatures beyond its Curie point or max rated temperature, it will irreversibly lose magnetism—thus compromising connector functionality.
B. Degradation of Contact Materials
Magnetic connectors use conductive contacts (often pogo pins) for signal and power transmission. These contacts are typically made of copper alloys, beryllium copper (BeCu), or phosphor bronze and plated with gold or nickel for corrosion resistance and conductivity.
Under high temperatures:
The elasticity of spring-loaded pins may degrade.
Plating materials may oxidize or wear off, increasing contact resistance.
The connector housing may soften or warp if made of low-grade thermoplastics.
C. Thermal Expansion Mismatch
Differential thermal expansion between various materials (metal pins, plastic housing, magnets, PCB mount) can cause:
Stress at interfaces.
Microcracks or warping.
Misalignment of contact points.
D. Insulation Breakdown and Fire Risk
Plastic insulation, seals, and encapsulating materials may degrade, emit fumes, or even catch fire under extreme temperatures if they are not appropriately rated.
2. Key Design Considerations for High-Temperature Magnetic Connectors
To ensure magnetic connectors function reliably in elevated temperature conditions, manufacturers must consider multiple design parameters:
A. Use of High-Temperature Magnets
Choosing the right type of permanent magnet is crucial:
SmCo magnets are ideal for high-heat applications, despite their higher cost.
High-grade NdFeB (e.g., N35SH, N42EH) can withstand temperatures up to 150°C or even 200°C in special formulations.
The shape and encapsulation of the magnet can also improve thermal tolerance.
B. Heat-Resistant Contact Materials
Beryllium copper and nickel-silver alloys are often preferred for high-temperature springs and contacts due to their fatigue resistance and thermal stability.
Gold plating over nickel base layers helps prevent oxidation and maintains low contact resistance over thermal cycling.
C. High-Temperature Polymers for Housing
The plastic or polymer housing must resist thermal deformation:
Common materials include PPS (polyphenylene sulfide), PEEK (polyether ether ketone), or LCP (liquid crystal polymer)—all capable of withstanding temperatures above 150°C.
Flame retardant grades should be used in safety-critical applications.
D. Thermal Expansion Accommodation
Use compliant design features (like floating contacts or flexible mounts).
Avoid sharp interfaces between materials with vastly different coefficients of thermal expansion (CTE).
E. Heat Dissipation Design
Integrate thermal vias or heat spreaders in the PCB layout.
Design air gaps or thermal isolation zones around the connector.
3. Applications Where High-Temperature Magnetic Connectors Are Essential
A. Automotive Electronics
Components under the hood (e.g., battery management systems, sensors, electric vehicle charging ports) can face operating temperatures above 125°C. Connectors must meet AEC-Q200 and ISO 16750 standards.
B. Industrial Machinery
Connectors in robotic arms, welding equipment, or extrusion machines often face both high temperatures and vibration. Magnetic connectors provide quick-disconnect capabilities without sacrificing robustness.
C. Aerospace and Defense
In avionics or satellite systems, connectors are exposed to extreme temperatures, radiation, and vacuum. Here, thermal stability is critical over long mission durations.
D. Medical Sterilization Equipment
Connectors on reusable surgical tools or diagnostic probes must withstand autoclave sterilization (typically 121–135°C with saturated steam). Only materials with thermal endurance and corrosion resistance can survive these cycles.
4. Reliability Testing for High-Temperature Performance
To validate magnetic connectors for thermal environments, manufacturers typically perform:
Thermal aging: Sustained exposure to 150–200°C to test material integrity.
Thermal cycling: Repeated heating and cooling from –40°C to +125°C to simulate real-world use.
Salt spray testing: High-temp corrosion test for humid or marine environments.
Electrical resistance monitoring: Check for contact degradation or intermittent failure.
Mechanical endurance under heat: Ensure pogo pin force and retention don’t degrade after thermal exposure.
5. Real-World Performance Expectations
With correct design and material choices, magnetic connectors can indeed function reliably in high-temperature environments, provided:
Temperature thresholds are known and not exceeded.
Materials and magnet grades are selected based on application specs.
Connectors are adequately validated via thermal tests.
Many industrial-grade connectors on the market today support operating ranges from –40°C to +150°C, and specialty aerospace or medical versions can go even higher.
6. Future Developments
To enhance high-temperature performance, the following trends are expected:
Magnet innovation: Development of rare-earth magnets with higher Curie temperatures and lower degradation.
Advanced coatings: Use of nanocoatings to resist oxidation and thermal wear.
Smart connectors: Integrating temperature sensors into the connector to monitor and report thermal stress.
Miniaturization with heat resilience: Designing compact connectors that can still manage heat effectively.
Magnetic connectors can absolutely be designed to operate in high-temperature environments, but not all magnetic connectors are inherently suitable for such conditions. Without the correct selection of magnets, contact materials, and housing polymers, their performance may degrade or even fail under thermal stress.
Designers must understand the application's temperature requirements and carefully balance thermal resistance, magnetic retention, mechanical robustness, and cost. With the proper engineering and validation, magnetic connectors can meet or exceed the demands of high-temperature applications in automotive, aerospace, industrial, and medical sectors.
In short, while standard consumer-grade magnetic connectors may not survive high-heat environments, industrial- or military-grade magnetic connectors can be engineered to thrive in them—making them a powerful, versatile solution for challenging thermal applications.